ПРИЛОЖЕНИЕ С (рекомендуемое) КРИТЕРИИ ОЦЕНКИ КАЧЕСТВА ГРУППЫ ДЕФЕКТОВ
(Извлечение из методики ультразвукового контроля качества сварных стыковых соединений
полиэтиленовых газопроводов АО "ВНИИСТ")
Группа дефектов – ПРОТЯЖЕННЫЕ
Несплавления, цепочки и скопления пор, включений
Таблица С.1
Критерии оценки качества |
Условное обозначение труб SDR11 |
Ø63 ×5,8 |
Ø75 ×6,8 |
Ø90 ×8,2 |
Ø110 ×10 |
Ø125 ×11,4 |
Ø140 ×12,7 |
Ø160 ×14,6 |
Ø180 ×16,4 |
Ø200 ×18,2 |
Ø225 ×20,5 |
Ø250 ×22,7 |
Ø280 ×25,4 |
Ø315 ×28,6 |
Максимально допустимая площадь, мм 2 |
0,78 |
1,09 |
1,58 |
2,37 |
3,05 |
3,08 |
5,0 |
5,56 |
6,82 |
8,68 |
13,36 |
16,75 |
21,22 |
Диаметр плоскодонного отверстия, мм |
1,1 |
1,3 |
1,7 |
1,8 |
2,1 |
2,3 |
2,6 |
3,0 |
3,3 |
3,4 |
3,7 |
4,2 |
4,7 |
Условная протяженность дефекта, мм |
10 |
10 |
20 |
20 |
30 |
30 |
30 |
30 |
30 |
30 |
30 |
30 |
30 |
Допустимое количество дефектов на периметре стыка, мм |
3 |
3 |
2 |
3 |
2 |
2 |
2 |
3 |
3 |
3 |
4 |
4 |
5 |
Таблица С.2
Критерии оценки качества |
Условное обозначение труб SDR17,6 |
SDR9 |
SDR7,4 |
Ø90 ×5,1 |
Ø110 ×6,3 |
Ø125 ×7,1 |
Ø140 ×8,0 |
Ø160 ×9,1 |
Ø180 ×10,3 |
Ø200 ×11,4 |
Ø225 ×12,8 |
Ø250 ×14,2 |
Ø280 ×15,9 |
Ø315 ×17,9 |
Ø180 ×20,0 |
Ø110 ×15,1 |
Ø160 ×21,9 |
Ø225 ×30,8 |
Максимально допустимая площадь, мм 2 |
1,02 |
1,48 |
1,9 |
2,4 |
3,13 |
4,0 |
4,88 |
6,16 |
7,89 |
9,89 |
12,52 |
7,25 |
3,12 |
6,61 |
9,98 |
Диаметр плоскодонного отверстия, мм |
1,2 |
1,4 |
1,6 |
1,8 |
2,1 |
2,4 |
2,6 |
2,9 |
3,3 |
3,6 |
4,1 |
3,3 |
2,2 |
3,2 |
4,6 |
Протяженность дефекта, мм |
10 |
10 |
10 |
20 |
20 |
20 |
20 |
30 |
30 |
30 |
30 |
30 |
30 |
30 |
30 |
Допустимое количество дефектов на периметре стыка, мм |
5 |
6 |
6 |
4 |
4 |
4 |
5 |
4 |
4 |
4 |
5 |
3 |
2 |
3 |
4 |
Группа дефектов – ОДИНОЧНЫЕ
Поры, механические включения (примеси)
Таблица С.3
Критерии оценки качества |
Условное обозначение труб SDR11 |
Ø63 ×5,8 |
Ø75 ×6,8 |
Ø90 ×8,2 |
Ø110 ×10 |
Ø125 ×11,4 |
Ø140 ×12,7 |
Ø160 ×14,6 |
Ø180 ×16,4 |
Ø200 ×18,2 |
Ø225 ×20,5 |
Ø250 ×22,7 |
Ø280 ×25,4 |
Ø315 ×28,6 |
Максимально допустимая площадь, мм 2 |
0,78 |
1,09 |
1,58 |
2,37 |
3,05 |
3,08 |
5,0 |
5,56 |
6,82 |
8,68 |
13,36 |
16,75 |
21,22 |
Диаметр плоскодонного отверстия, мм |
1,1 |
1,3 |
1,7 |
1,8 |
2,1 |
2,3 |
2,6 |
3,0 |
3,3 |
3,4 |
3,7 |
4,2 |
4,7 |
Условная протяженность дефекта, мм |
5 |
5 |
10 |
10 |
10 |
15 |
15 |
15 |
15 |
15 |
15 |
15 |
15 |
Допустимое количество дефектов на периметре стыка, мм |
6 |
6 |
5 |
6 |
6 |
5 |
5 |
6 |
7 |
7 |
8 |
9 |
10 |
Таблица С.4
Критерии оценки качества |
Условное обозначение труб SDR17,6 |
SDR9 |
SDR7,4 |
|
Ø90 ×5,1 |
Ø110 ×6,3 |
Ø125 ×7,1 |
Ø140 ×8,0 |
Ø160 ×9,1 |
Ø180 ×10,3 |
Ø200 ×11,4 |
Ø225 ×12,8 |
Ø250 ×14,2 |
Ø280 ×15,9 |
Ø315 ×17,9 |
Ø180 ×20,0 |
Ø110 ×15,1 |
Ø160 ×21,9 |
Ø225 ×30,8 |
Максимально допустимая площадь, мм 2 |
1,02 |
1,48 |
1,9 |
2,4 |
3,13 |
4,0 |
4,88 |
6,16 |
7,89 |
9,89 |
12,52 |
7,25 |
3,12 |
6,61 |
9,98 |
Диаметр плоскодонного отверстия, мм |
1,2 |
1,4 |
1,6 |
1,8 |
2,1 |
2,4 |
2,6 |
2,9 |
3,3 |
3,6 |
4,1 |
3,3 |
2,2 |
3,2 |
4,6 |
Протяженность дефекта, мм |
5 |
5 |
5 |
5 |
10 |
10 |
10 |
15 |
15 |
15 |
15 |
15 |
15 |
15 |
15 |
Допустимое количество дефектов на периметре стыка, мм |
9 |
10 |
10 |
10 |
8 |
9 |
10 |
8 |
8 |
9 |
10 |
6 |
4 |
5 |
8 |
Примечания (к таблицам С.1-С.4):
1. Максимально допустимая площадь определяется по формуле 0,00075 SП/ K; диаметр плоскодонного отверстия в СОП
определяется из выражения , где S – толщина стенки трубы,
мм; D – диаметр трубы, мм; П – периметр трубы, мм; K – поправочный коэффициент: для SDR17,6 K=1,0;
для SDR11
K=0,9 при S <10,0
K=1,0 при 10,0< S <20,0
K=1,3 при S >20,0.
2. Следует различать два понятия: условная протяженность дефекта Lупи длина дефекта L. Условная
протяженность дефекта является амплитудно-временной характеристикой ультразвукового контроля и прямо пропорциональна
длине дефекта: L=LупK. Условная протяженность дефекта измеряется по длине дефектной зоны между крайними
положениями УЗ-преобразователя, при которых амплитуда эхо-сигнала достигает поискового уровня чувствительности. |
ПРИЛОЖЕНИЕ Т (рекомендуемое
МЕТОДИКА ИСПЫТАНИЙ СВАРНЫХ МУФТОВЫХ СОЕДИНЕНИЙ НА СПЛЮЩИВАНИЕ
Для определения стойкости муфтовых соединений к сплющиванию подготавливаются патрубки с
расположенными по центру муфтами, изображенные на рисунке Т.1. Длина патрубка и количество образцов, изготавливаемых из
каждого патрубка, должны соответствовать таблице Т.1.

Рисунок T.1 – Общий вид образцов-сегментов
Таблица Т.1
Номинальный диаметр труб с dн, мм |
Длина свободной части образца L, мм, не менее |
Количество образцов из одного патрубка, шт. |
Угол сегмента, град. |
20-75 |
3dн |
2 |
180 |
90-125 |
2 dн |
4 |
90 |
140-225 |
dн |
8 |
45 |
Не ранее чем через 24 ч после сварки производят разрезание сварного муфтового соединения вдоль оси
на испытательные образцы-сегменты в диаметральном сечении.
Испытания проводят при температуре (23±5) °С. При указанной температуре образцы выдерживают не менее 2 ч.
Для испытаний применяют механизированный процесс, обеспечивающий сближение плит со скоростью (100±10) мм/мин;
допускается использование пресса со скоростью сближения плит (20±2) мм/мин.
Подготовленный к испытанию образец устанавливают между обжимными плитами пресса так, как показано на рисунке Т.2. Затем осуществляют сближение обжимных плит до тех пор, пока расстояние между ними не сократится до удвоенной толщины стенки трубы.
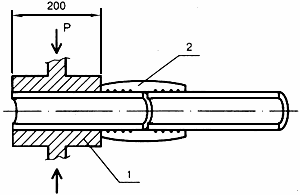
1 – обжимные плиты; 2 – испытываемый образец
Рисунок Т.2 – Схема испытания образцов-сегментов на сплющивание
Допускается проведение испытаний с использованием обжимных плит без округления кромок. В этом случае
в начале испытания расстояние от торца соединительной детали до торца губок должно быть (20±3) мм.
При согласовании с заказчиком допускается испытание образцов соединений труб диаметром до 63 мм включительно производить
в слесарных тисках по ГОСТ 4045 плавным деформированием образца.
После снятия нагрузки образец извлекают из пресса или тисков и визуально осматривают, определяя наличие отрыва трубы от
муфты или соединительной детали.
В случае если на части длины шва обнаружен отрыв трубы или соединительной детали от муфты, штангенциркулем по ГОСТ 166
измеряют длину части шва, не подвергнутой отрыву, и расстояние между крайними витками закладного нагревателя в зоне
сварки в пределах одной трубы, которое принимают за длину шва. Длина шва, не подвергнутая отрыву при сплющивании
Cc, %, определяется по формуле
где l – длина шва, не подверженная отрыву, мм;
L – длина зоны сварки (длина шва) в пределах одной трубы, определяемая по расстоянию
между крайними витками спирали закладного нагревательного элемента, мм.
Для удобства измерения допускается дополнительное разрезание образца любым режущим инструментом в продольном и
поперечном направлениях.
|