6.70 Технологический процесс соединения труб с помощью соединительных деталей с закладными нагревателями включает (рисунок 12): – подготовку концов труб (очистка от загрязнений, механическая обработка – циклевка свариваемых поверхностей, разметка и обезжиривание); – сборку стыка (установка и закрепление концов свариваемых труб в зажимах позиционера (центрирующего приспособления) с одновременной посадкой детали с ЗН, подключение детали с ЗН к сварочному аппарату); – сварку (задание программы процесса сварки, пуск процесса сварки, нагрев, охлаждение соединения).
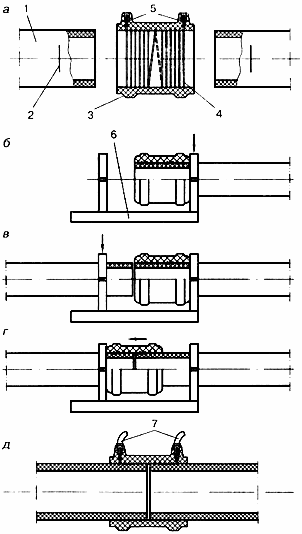
а – подготовка соединяемых элементов; б, в, г – этапы сборки стыка; д – собранный под сварку стык;
1 – труба; 2 – метка посадки муфты и механической обработки поверхности трубы; 3 – муфта; 4 – закладной нагреватель; 5 – клеммы токопровода; 6 – позиционер; 7 – токоподводящие кабели сварочного аппарата
Рисунок 12 – Схема соединения труб муфтой с закладным нагревателем
Для исключения неправильного распределения тепла внутри соединения, приводящего к сильному расплавлению полиэтилена, не рекомендуется превышать величину косого среза торца трубы а (рисунок 13), указанную в таблице 11.
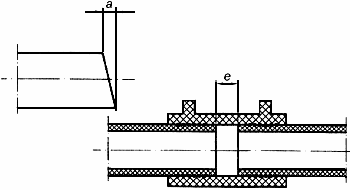
а – максимальный допуск косого среза трубы; e – максимальный зазор между двумя концами труб в муфте
Рисунок 13 Таблица 11
Диаметр, мм |
20-40 |
50 |
63 |
75 |
90 |
110 |
125 |
140 |
160 |
180 |
200 |
225 |
250 |
280 |
315 |
α |
2 |
2 |
3 |
3 |
4 |
5 |
6 |
6 |
7 |
7 |
8 |
8 |
9 |
9 |
10 |
β |
— |
5 |
7 |
8 |
9 |
11 |
13 |
14 |
16 |
17 |
18 |
20 |
22 |
23 |
24 |
Очистку концов труб от загрязнений производят так же, как при выполнении сварки встык. Концы труб, защищенных полипропиленовой оболочкой, освобождаются от нее с помощью специального ножа. Длина очищаемых концов труб должна быть, как правило, не менее 1,5 длины раструбной части применяемых для сварки деталей. Механическую обработку поверхности концов свариваемых труб производят на длину, равную не менее 0,5 длины используемой детали. Она заключается в снятии слоя толщиной 0,1-0,2 мм с поверхности размеченного конца трубы. Для труб диаметром до 75 мм, а также для удаления заусенец с торца трубы, как правило, применяется ручной скребок (цикля). Для труб диаметром более 75 мм, а также для труб, изготовленных из ПЭ 100 независимо от диаметра, рекомендуется использовать механический инструмент (торцовочную оправку), которая обеспечивает быстрое и равномерное снятие оксидного слоя с поверхности труб. Кольцевой зазор между трубой и соединительной деталью не должен, как правило, превышать 0,3 мм и после сборки на трубе должны быть видны следы механической обработки поверхности. Для правильной центровки соединения после механической обработки на концы свариваемых труб наносят метки глубины посадки муфты (соединительной детали), равные половине ее длины. Не рекомендуется превышать величину зазора между торцами труб в муфте е (рисунок 13), указанный в таблице 11. Свариваемые поверхности труб после циклевки и муфты обезжиривают путем протирки салфеткой из хлопчатобумажной ткани, смоченной в спирте или других специальных обезжиривающих составах, которые полностью испаряются с поверхности. Детали с закладными нагревателями, поставляемые изготовителем в индивидуальной герметичной упаковке, вскрываемой непосредственно перед сборкой, обезжириванию допускается не подвергать. Механическую обработку и протирку труб и деталей производят непосредственно перед сборкой и сваркой. Детали с закладными нагревателями механической обработке не подвергаются. 6.71 Сборка стыка заключается в посадке муфты на концы свариваемых труб с установкой по ранее нанесенным меткам, по ограничителю или по упору в позиционере. Рекомендуется для сборки стыков труб, поставляемых в отрезках, использовать центрирующие хомуты и позиционеры, а для сборки стыков труб, проставляемых в бухтах или на катушках, использовать выпрямляющие позиционеры. Процесс сборки включает: – надевание муфты на конец первой трубы до совмещения торцов муфты и трубы, закрепление конца трубы в зажиме позиционера (рисунок 12, б); – установку в упор в торец первой трубы и закрепление конца второй трубы в зажиме позиционера (рисунок 12, в); – надвижение муфты на конец второй трубы на 0,5 длины муфты до упора в зажим позиционера (рисунок 12, г) или до метки, нанесенной на трубу; – подключение к клеммам муфты токоподводящих кабелей от сварочного аппарата (рисунок 12, д). В случае если муфты имеют внутренний ограничитель (кольцевой уступ), то сборка труб производится до упора торцов труб в кольцевой уступ и собранное соединение закрепляется в позиционере. Если свариваемые концы труб имеют овальность больше 1,5% наружного диаметра трубы или 1,5 мм, то перед сборкой стыка для придания им округлой формы используют инвентарные калибрующие зажимы, которые устанавливают на трубы на удалении 15-30 мм от меток или устраняют овальность при помощи специальных приспособлений. Во избежание повреждения закладных нагревателей (проволочных электроспиралей) надевание детали с ЗН на конец трубы или введение конца трубы в муфту производят без перекосов. Концы труб, входящие в соединительные детали, не должны находиться под действием изгибающих напряжений и под действием усилий от собственного веса. Муфты после монтажа должны свободно вращаться на концах труб от нормального усилия руки. 6.72 Трубы сваривают при обеспечении неподвижности соединения в процессе нагрева и последующего естественного охлаждения. Параметры режимов сварки устанавливают в зависимости от вида и сортамента используемых соединительных деталей с ЗН и (или) сварочных аппаратов в соответствии с указаниями заводов-изготовителей в паспортах изделий. При включении аппарата процесс сварки происходит в автоматическом режиме. В паспорте детали с ЗН или на штрих-коде указываются время охлаждения сварного соединения до той температуры, при которой это соединение можно перемещать, и время охлаждения до той температуры, при которой возможно нагружение газопровода опрессовочным или рабочим давлением. 6.73 Приварку к трубам седловых отводов производят в следующей последовательности: – размечают место приварки отвода на трубе (рисунок 14); – поверхность трубы в месте приварки отвода зачищают с помощью цикли; – привариваемую поверхность отвода обезжиривают, а если он поставляется изготовителем в герметичной индивидуальной упаковке, вскрываемой непосредственно перед сборкой, то его обезжириванию допускается не подвергать; – отвод устанавливают на трубу и механически прикрепляют с помощью специальных зажимов, хомутов и т.п. (рисунок 14); – если труба в зоне приварки отвода имеет повышенную овальность (больше 1,5% наружного диаметра трубы или 1,5 мм), то перед установкой отвода трубе придают правильную геометрическую форму с помощью калибрующих зажимов, укрепляемых на трубе на расстоянии 15-30 мм от меток (зажимы снимают только после сварки и охлаждения соединения); – подключают к контактным клеммам токоподвода сварочные кабели; – производят сварку; – после окончания сварки и охлаждения перед фрезерованием трубы производят визуальный контроль качества сварного соединения. Рекомендуется для проверки качества сварки через патрубок приваренного отвода подать избыточное давление воздуха внутрь седлового отвода с одновременным обмыливанием места примыкания основания отвода к газопроводу; – производят фрезерование стенки трубы для соединения внутренних полостей отвода и трубы после полного охлаждения соединения.
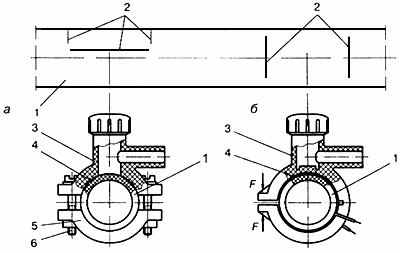
а – седловой отвод с закладным нагревателем; б – отвод с разрезной муфтой с закладным нагревателем;
1 – труба; 2 – метки посадки отводов и механической обработки поверхности трубы; 3 – отвод; 4 – закладной нагреватель; 5 – полухомут; 6 – винты крепления; F– усилие прижатия отвода при сборке и сварке
Рисунок 14 – Соединение полиэтиленовой трубы и отводов с закладными нагревателями
Технология соединения полиэтиленовых труб со стальными 6.74 Полиэтиленовые втулки под фланцы, используемые для изготовления разъемных соединений "полиэтилен-сталь", соединяют с трубами сваркой встык нагретым инструментом или при помощи муфт с закладными нагревателями. 6.75 При сварке втулок под фланцы с полиэтиленовыми трубами применяют сварочные устройства, оснащенные приспособлениями для центровки и закрепления втулок. 6.76 Рекомендуется сборку и сварку втулок под фланцы с трубами производить в условиях мастерских. При этом втулку приваривают к патрубку длиной не менее 0,8-1,0 м (рисунок 15).
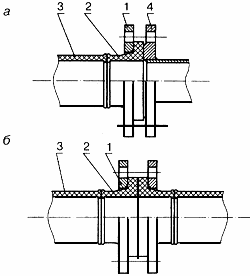
а – полиэтиленовых труб со стальными трубами, арматурой; б – полиэтиленовых труб между собой;
1 – фланец стальной свободный; 2 – втулка под фланец из полиэтилена; 3 – труба из полиэтилена; 4 – фланец стальной трубы, арматуры
Рисунок 15 – Фланцевые соединения
6.77 Перед приваркой готового узла (втулка-патрубок) или отдельной втулки под фланец к трубе на замыкающем участке газопровода рекомендуется предварительно надеть на трубу свободный фланец. 6.78 При сборке фланцевых соединений затяжку болтов производят поочередно, завинчивая противоположно расположенные гайки тарированным или динамометрическим ключом с усилием, регламентированным технологической картой. Гайки болтов располагают на одной стороне фланцевого соединения. Размеры фланцев приведены в приложении К. 6.79 При вварке неразъемных соединений "полиэтилен-сталь" в трубопровод вначале производят сборку и сварку труб из полиэтилена, затем осуществляют сборку и сварку стыка стальных труб. Рекомендуется производить сварку перехода "полиэтилен-сталь" вначале к отрезку стальной трубы длиной до 1 м в условиях мастерских, где можно обеспечить температурные условия для зоны раструбного перехода. При подгонке стальных труб в захлесте газовую резку и шлифовку кромки следует производить на конце стального трубопровода, а не стального патрубка переходника. В процессе подгонки и сборки стыка, выполнения прихваток и последующей электродуговой сварки полиэтиленовый патрубок должен быть защищен от брызг металла и шлака. При электродуговой сварке стыка зона раструбного перехода "полиэтилен-сталь" не должна нагреваться более 50°С. Контроль качества сварки стыка стальных труб должен осуществляться в соответствии с требованиями СНиП 42-01. Типы соединений "полиэтилен-сталь" и их размеры приведены в приложении К. Вварка трубной полиэтиленовой вставки в трубопровод, уложенный в траншею 6.80 В траншее трубные вставки вваривают в следующих случаях: – при замыкании участков строящихся трубопроводов; – при врезке ответвлений в ранее построенный газопровод; – при выявлении некачественных сварных соединений. 6.81 Трубные вставки вваривают при помощи муфт с закладными нагревателями в газопроводы диаметром от 20 мм до 315 мм или сваркой встык нагретым инструментом в газопроводы диаметром от 63 мм до 160 мм, в обоснованных случаях – до 225 мм. 6.82 При вварке трубной вставки нагретым инструментом встык работы выполняют в следующем порядке: – определяют местонахождение повреждения или дефекта трубопровода; – освобождают от грунтовой присыпки участок трубопровода необходимой длины; – расширяют траншею в зоне производства работ и делают приямок для размещения сварочного оборудования; – очищают, размечают и вырезают поврежденный или заменяемый участок; – от цельной трубы отрезают вставку требуемого размера; – приваривают вставку к первому (с меньшей длиной освобождения) концу трубопровода; – приваривают второй конец трубопровода (с большей длиной освобождения) к вставке с одновременным упругим изгибом трубопровода методом подъема для обеспечения осевого перемещения конца при сварке встык нагретым инструментом.
|