4. СБОРКА, СВАРКА И КОНТРОЛЬ КАЧЕСТВА СВАРНЫХ СОЕДИНЕНИИ ТРУБОПРОВОДОВ
Общие положения
4.1. Перед сборкой и сваркой труб необходимо:
произвести визуальный осмотр поверхности труб (при этом трубы не должны иметь недопустимых дефектов, регламентированных техническими условиями на поставку труб);
очистить внутреннюю полость труб от попавшего внутрь грунта, грязи, снега;
выправить или обрезать деформированные концы и повреждения поверхности труб;
очистить до чистого металла кромки и прилегающие к ним внутреннюю и наружную поверхности труб на ширину не менее 10 мм.
При стыковой сварке оплавлением следует дополнительно зачищать торец трубы и пояс под контактные башмаки сварочной машины.
4.2. Допускается правка плавных вмятин на торцах труб глубиной до 3,5 % диаметра труб и деформированных концов труб безударными разжимными устройствами. При этом на трубах из сталей с нормативным временным сопротивлением разрыву до 539 МПа (55 кгс/мм2) допускается правка вмятин и деформированных концов труб при положительных температурах без подогрева. При отрицательных температурах окружающего воздуха необходим подогрев на 100–150°С. На трубах из сталей с нормативным временным сопротивлением разрыву 539 МПа (55 кгс/мм2) и выше – с местным подогревом на 150-200° С при любых температурах окружающего воздуха.
Участки и торцы труб с вмятиной глубиной более 3,5 % диаметра трубы или имеющие надрывы необходимо вырезать.
Допускается ремонт сваркой забоин и задиров фасок глубиной до 5 мм.
Концы труб с забоинами и задирами фасок глубиной более 5 мм следует обрезать.
4.3. Сборка труб диаметром 500 мм и более должна производиться на внутренних центраторах. Трубы меньшего диаметра можно собирать с использованием внутренных или наружных центраторов. Независимо от диаметра труб сборка захлестов и других стыков, где применение внутренних центраторов невозможно производится с применением наружных центраторов.
4.4. При сборке труб с одинаковой нормативной толщиной стенки смещение кромок допускается на величину до 20 % толщины стенки трубы, но не более 3 мм при дуговых методах сварки и не более 2 мм при стыковой сварке оплавлением.
4.5. Непосредственное соединение на трассе разнотолщинных труб одного и того же диаметра или труб с деталями (тройниками, переходами, днищами, отводами) допускается при следующих условиях:
если разность толщин стенок стыкуемых труб или труб с деталями (максимальная из которых 12 мм и менее) не превышает 2,5 мм;
если разность толщин стенок стыкуемых труб или труб с деталями (максимальная из которых более 12 мм) не превышает 3 мм.
Соединение труб или труб с деталями с большей разностью толщин стенок осуществляется путем вварки между стыкуемыми трубами или трубами с дeтaлями переходников или вставок промежуточной толщины, длина которых должна быть не менее 250 мм.
При разнотолщинности до 1,5 толщины допускается непосредственная сборка и сварка труб при специальной разделке кромок более толстой стенки трубы или детали. Конструктивные размеры разделки кромок и сварных швов должны соответствовать указанным на рис. 1.
Смещение кромок при сварке разностенных труб, измеряемое по наружной поверхности, не должно превышать допусков, установленных требованиями п. 4.4 настоящего раздела.
Подварка изнутри корня шва разностенных труб диаметром 1000 мм и более по всему периметру стыка обязательна, при этом должен быть очищен подварочный слой от шлака, собраны и удалены из трубы огарки электродов и шлак.
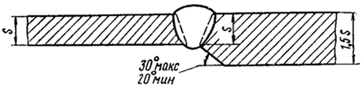
Рис. 1. Конструктивные размеры разделки кромок и сварных швов разнотолщинных труб (до 1,5 толщины стенки)
4.6. Каждый стык должен иметь клеймо сварщика или бригады сварщиков, выполняющих сварку. На стыки труб из стали с нормативным временным сопротивлением разрыву до 539 МПа (55 кгс/мм2) клейма должны наноситься механическим способом или наплавкой. Стыки труб из стали с нормативным временным сопротивлением разрыву 539 МПа (55 кгс/мм2) и выше маркируются несмываемой краской снаружи трубы.
Клейма наносятся на расстоянии 100-150 мм от стыка в верхней полуокружности трубы.
4.7. Приварка каких-либо элементов, кроме катодных выводов, в местах расположения поперечных кольцевых, спиральных и продольных заводских сварных швов, не допускается. В случае если проектом предусмотрена приварка элементов к телу трубы, то расстояние между швами трубопровода и швом привариваемого элемента должно быть не менее 100 мм.
4.8. Непосредственное соединение труб с запорной и распределительной арматурой разрешается при условии, что толщина свариваемой кромки патрубка арматуры не превышает 1,5 толщины стенки стыкуемой с ней трубы в случае специальной подготовки кромок патрубка арматуры в заводских условиях согласно рис. 2.
Во всех случаях, когда специальная разделка кромок патрубка арматуры выполнена не в заводских условиях, а также когда толщина свариваемой кромки патрубка арматуры превышает 1,5 толщины стенки стыкуемой с ней трубы, соединение следует производить путем вварки между стыкуемой трубой и арматуpoй специального переходника или переходного кольца.
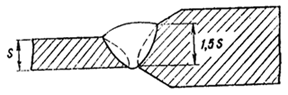
Рис. 2. Подготовка промок патрубков арматуры при непосредственном соединении их с трубами
4.9. При сварке трубопровода в нитку сварные стыки должны быть привязаны к пикетам трассы и зафиксированы в исполнительной документации.
4.10. При перерыве в работе более 2 ч концы свариваемого участка трубопровода следует закрыть инвентарными заглушками для предотвращения попадания внутрь трубы снега, грязи и т. п.
4.11. Кольцевые стыки стальных магистральных трубопроводов могут свариваться дуговыми методами сварки или стыковой сваркой оплавлением.
4.12. Допускается выполнение сварочных работ при температуре воздуха до минус 50°С.
При ветре свыше 10 м/с, а также при выпадении атмосферных осадков производить сварочные работы без инвентарных укрытий запрещается.
4.13. Монтаж трубопроводов следует выполнять только на инвентарных подкладках. Применение грунтовых и снежных призм для монтажа трубопровода не допускается.
4.14. К прихватке и сварке магистральных трубопроводов допускаются сварщики, сдавшие экзамены в соответствии с Правилами аттестации сварщиков Госгортехнадзора СССР, имеющие удостоверения и выдержавшие испытания, регламентируемые требованиями пп. 4.16-4.23 настоящего раздела.
4.15. Изготовление сварных соединительных деталей трубопровода (отводов, тройников, переходов и др.) в полевых условиях запрещается.
ПРОВЕРКА КВАЛИФИКАЦИИ СВАРЩИКОВ
4.16. При производстве сварочных работ каждый сварщик (бригада или звено сварщиков в случае сварки стыка бригадой или звеном) должен (должны) сварить допускной стык для труб диаметром до 1000 мм
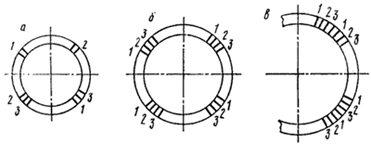
Рис. 3. Схема вырезки образцов для механических испытаний
а – трубы диаметром от 400 мм до 1000 мм; в – трубы диаметром 1000 мм и более; 1 – образец для испытания на растяжение (ГОСТ 6996-66, тип XII или XIII); 2 – образец на изгиб корнем шва наружу (ГОСТ 6996-66, тип XXVII или XXVIII) или на ребро; 3 – образец на изгиб корнем шва внутрь (ГОСТ 6996-66, тип XXVII или XXVIII) или на ребро
или половину стыка для труб диаметром 1000 мм и более в условиях, тождественных с условиями сварки на трассе, если:
он (они) впервые приступил (и) к сварке магистрального трубопровода или имел (и) перерыв в своей работе более трех месяцев;
сварка труб осуществляется из новых марок сталей или с применением новых сварочных материалов, технологии и оборудования;
изменился диаметр труб под сварку (переход от одной группы диаметров к другой – см. группы а, б, в на рис. 3);
изменена форма разделки торцов труб под сварку.
Допускной стык подвергается:
визуальному осмотру и обмеру, при котором сварной шов должен удовлетворять требованиям пп. 4.26; 4.27 настоящего раздела;
радиографическому контролю в соответствии с требованиями п.4.28 настоящего раздела;
механическим испытаниям образцов, вырезанных из сварного соединения в соответствии с требованиями п. 4.19 настоящего раздела.
4.18. Если стык по визуальному осмотру и обмеру или при радиографическим контроле не удовлетворяет требованиям пп.4.26, 4.27, 4.32 настоящего раздела, то производится сварка и повторный контроль двух других допускных стыков; в случае получения при повторном контроле неудовлетворительных результатов хотя бы на одном из стыков бригада или отдельный сварщик признаются не выдержавшими испытание.
4.19. Механическими испытаниями предусматривается проверка образцов на растяжение и на изгиб, вырезанных из сварных соединений. Схема вырезки и необходимое количество образцов для различных видов механических испытаний должны соответствовать указанным на рис. 3 и в табл. 3.
Таблица 3
диаметр трубы, мы |
Количество образцов для механических испытаний |
на растяжение |
на изгиб с расположением корпя шва |
всего |
наружу |
внутрь |
на ребро |
|
Толщина стенки, трубы до 12,5 мм включительно |
До 400 мм |
2 |
2 |
2 |
— |
6 |
Свыше 400 мм |
4 |
4 |
4 |
— |
12 |
Толщина стенки трубы свыше 12,5 мм |
До 400 мм |
2 |
— |
— |
4 |
6 |
Свыше 400 мм |
4 |
— |
— |
8 |
12 |
Образцы для проведения механических испытаний должны быть подготовлены в соответствии с требованиями ГОСТ 6996-66 и настоящей главы.
4.20. Временное сопротивление разрыву сварного соединения, определенное на разрывных образцах со снятым усилением, должно быть не меньше нормативного значения временного сопротивления разрыву металла труб.
4.21. Среднее арифметическое значение угла изгиба образцов, сваренных дуговыми методами сварки, должно быть не менее 120°, а его минимальное значение – не ниже 100°.
4.22. Среднее арифметическое значение угла изгиба образцов, сваренных стыковой сваркой оплавлением, должно быть не менее 70°, а его минимальное значение – не ниже 40°. При подсчете среднего значения все углы больше 110° принимаются равными 110°.
4.23. Если образцы, вырезанные из стыка, имеют неудовлетворительные показатели механических свойств согласно требованиям пп. 4.20-4.22 настоящего раздела, то испытания проводятся на удвоенном количестве образцов, вырезанных из повторно сваренного стыка; в случае получения при повторном испытании неудовлетворительных результатов бригада сварщиков или отдельный сварщик признаются не выдержавшими испытание и должны пройти переподготовку.
Контроль сварных соединений
4.24. Контроль сварных стыков трубопроводов производится:
систематическим операционным контролем, осуществляемым в процессе сборки и сварки трубопроводов;
визуальным осмотром и обмером сварных соединений;
проверкой сварных швов неразрушающими методами контроля;
по результатам механических испытаний сварных соединений в соответствии с п.4.29 настоящего раздела.
4.25. Операционный контроль должен выполняться производителями работ и мастерами, а самоконтроль – исполнителями работ.
При операционном контроле должно проверяться соответствие выполняемых работ рабочим чертежам, требованиям настоящего раздела, государственным стандартам и инструкциям, утвержденным в установленном порядке.
4.26. Стыки, выполненные дуговой сваркой, очищаются от шлака и подвергаются внешнему осмотру. При этом они не должны иметь трещин, подрезов глубиной более 0,5 мм, недопустимых смещений кромок, кратеров II выходящих на поверхность пор.
Усиление шва должно быть высотой в пределах от 1 до 3мм и иметь плавный переход к основному метал-.1 у.
4.27. Стыки, выполненные стыковой сваркой оплавлением, после снятия внутреннего и наружного грата должны иметь усиление высотой не более 3 мм. При снятии внутреннего и наружного грата не допускается уменьшение толщины стенки трубы.
Смещение кромок после сварки не должно превышать 25% толщины стенки, но не более 3 мм. Допускаются местные смещения на 20% периметра стыка, величина которых не превышает 30% толщины стенки, но не более 4 мм.
4.28. Монтажные сварные стыки трубопроводов и их участков всех категорий, выполненные дуговой сваркой, подлежат контролю физическими методами в объеме 100%, из них только радиографическим методом сварные стыки:
участков трубопроводов категорий B и I во всех районах и независимо от диаметра;
трубопроводов диаметром 1020-1420 мм и их участков в районах Западной Сибири и Крайнего Севера;
участков трубопроводов на переходах через болота II и III типа во всех районах;
участков трубопроводов на переходах через железные дороги и автомобильные дороги I, II и III категорий во всех районах;
трубопроводов на участках их надземных переходов, захлестов, ввариваемых вставок и арматуры.
участков трубопроводов, указанных в позициях 6, 9, 10, 18, 20 и 23 таблицы 3 СНиП 2.05.06-85
В остальных случаях монтажные сварные стыки трубопроводов и их участков подлежат контролю для категорий II, III и IV радиографическим методом в объеме соответственно не менее 25; 10 и 5%, а остальные сварные стыки – ультразвуковым или магнитографическим методом.
Угловые сварные стыки трубопроводов подлежат контролю ультрозвуковым методом в объеме 100%.
4.29. Сварные соединения трубопроводов 1, II, III, IV категорий, выполненные стыковой сваркой оплавлением, подвергаются:
100%-ному контролю физическими методами по зарегистрированным параметрам процесса сварки.
механическим испытаниям в объеме 1% стыков в соответствии с пп. 4.20, 4.22 настоящей главы с целью проверки состояния системы автоматического управления процессом сварки .
4.30. При неудовлетворительных результатах механических испытаний сварных стыков необходимо:
сварку прекратить, установить причину неудовлетворительного качества сварного стыка;
весь участок трубопровода, сваренный с момента последней проверки монтажной организацией в присутствии представителей технадзора заказчика, подвергнуть силовому воздейстиию на изгиб с созданием (в верхней II нижней частях каждого стыка) напряжения, равного 0,9 нормативного предела текучести.
Работа может быть продолжена данным сварщиком на той же установке только после настройки системы автоматического управления процессом и после получения удовлетворительных результатов дополнительно сваренного и проверенного допускного стыка в соответствии с требованиями пп. 4.17, 4.19, 4.20, 4.22.
Таблица 4
Категория участков трубопроводов |
Количество сварных стыков, подлежащих контролю физическими методами, % |
|
в том числе |
Всего |
радиографический |
магнитографический или ультразвуковой |
В |
100 |
100 |
— |
1 |
100 |
100 |
— |
II |
100 |
Не менее 25 |
Остальное |
III |
100 |
” ” 10 |
|
IV |
Не менее 20 |
” ” 5 |
|
IV (наземная и |
100 |
” ” 10 |
|
надземная прокладка) |
|
|
|
Угловые сварные швы |
100 |
— |
100 (ультразвуковым методом) |
Примечания: 1.Стыки трубопроводов надземных переходов, захлестов, ввариваемых вставок, арматуры контролируются в объеме 100% радиографическим методом.
2. Контролю не подвергаются сварные соединения труб и арматуры, выполненные заводами-поставщиками.
3. На участках IV категории подвергаются контролю стыки из числа наихудших по внешнему виду. |
4.31. Кроме установленных норм количества сварных соединений, подвергаемых контролю физическими методами и механическим испытаниям, проверке могут подвергаться также отдельные сварные соединения, назначаемые к контролю представителями технадзора заказчика, Госгазнадзора СССР и Государственной инспекции по качеству строительства.
4.32. При контроле физическими методами стыков трубопроводов, выполненных дуговыми способами сварки, годными считаются сварные швы, в которых:
отсутствуют трещины любой глубины и протяженности;
глубина шлаковых включений не превышает 10% толщины стенки трубы при их суммарной длине не более 1/6 периметра стыка;
наибольший из размеров пор в процентном отношении к толщине стенки трубы не превышает 20% при расстоянии между соседними порами не менее 3 толщин стенки; 15% при расстоянии между соседними порами не менее 2 толщин стенки; 10% при расстоянии между соседними порами менее 2 толщин стенки, но не менее 3-кратного размера поры; 10% при расстоянии между соседними порами менее З-кратного размера поры на участках общей длиной не более 30 мм на 500 мм шва.
Во всех случаях максимальный размер поры не должен превышать 2,7 мм.
Допускается местный непровар в корне шва глубиной до 10% толщины стенки трубы, но не более 1 мм, суммарной длиной до 1/6 периметра стыка.
В стыках трубопровода диаметром 1000 мм и более на участках, выполненных с внутренней подваркой, непровары в корне шва не допускаются.
Суммарная длина непровара по кромкам и между слоями в неповоротных стыках труб, выполненных автоматической дуговой сваркой, не должна превышать 50 мм на участке шва длиной 350 мм.
Суммарная глубина непровара и шлаковых включений, расположенных в одной плоскости, не должна превышать 10% толщины стенки трубы, но неболее 1 мм, при этом длина дефектного участка не должна превышать 50 мм на участке шва длиной 350 мм.
4.33. При неудовлетворительных результатах проверки физическими методами хотя бы одного стыка трубопроводов IV категории следует проверить тем же методом дополнительно 25% сваренных стыков из числа стыков, выполненных с момента предыдущей проверки. При этом сварщик или бригада, допустившие брак, от работы отстраняются до завершения проверки. Если при повторной проверке хотя бы одни стык окажется неудовлетворительного качества, сварщик или бригада, допустившие брак, к сварочным работам не допускаются до повторной сдачи испытаний, а сваренные ими стыки с момента предыдущей проверки подвергаются 100-ному радиографическому контролю.
4.34. Исправление дефектов в стыках, выполненных дуговыми методами сварки, допускается в следующих случаях:
если суммарная длина дефектных участков не превышает 1/6 периметра стыка;
если длина выявленных в стыке трещин не превышает 50 мм.
При наличии трещин суммарной длиной более 50 мм стыки подлежат удалению.
4.35. Исправление дефектов в стыках, выполненных дуговыми методами сварки, следует производить следующими способами:
подваркой изнутри трубы дефектных участков в корне шва;
наплавкой ниточных валиков высотой не более 3 мм при ремонте наружных и внутренних подрезов;
вышлифовкой и последующей заваркой участков швов со шлаковыми включениями и порами;
при ремонте стыка с трещиной длиной до 50 мм засверливаются два отверстия на расстоянии не менее 30 мм от краев трещины с каждой стороны, дефектный участок вышлифовывается полностью и заваривается вновь в несколько слоев;
обнаруженные при внешнем осмотре недопустимые дефекты должны устраняться до проведения контроля неразрушающими методами.
4.36. Все исправленные участки стыков должны быть подвергнуты внешнему осмотру, радиографическому контролю и удовлетворять требованиям п. 4.32 настоящего раздела. Повторный ремонт стыков не допускается.
4.37. Результаты проверки стыков физическими методами необходимо оформлять в виде заключений. Заключения, радиографические снимки, зарегистрированные результаты ультразвуковой дефектоскопии и ферромагнитные ленты со стыков, подвергавшихся контролю, хранятся в полевой испытательной лабаратории (ПИЛ) до сдачи трубопровода в эксплуатацию.
Изготовление и монтаж кривых поворота трубопровода
4.38. Повороты линейной части трубопровода в вертикальной и горизонтальной плоскостях следует выполнять упругим изгибом сваренной нитки трубопровода или монтажом криволинейных участков из гнутых отводов.
Если на отдельных участках трассы в соответствии с проектом необходимо выполнить повороты малого радиуса, который не может быть получен при изгибе труб на станках холодного гнутья и штампосварных отводов, выполненных в соответствии с главой СНиП по нормам проектирования магистральных трубопроводов.
4.39. Выполнение сварных косых стыков в полевых условиях запрещается.
4.40. Радиусы упругого изгиба трубопровода устанавливаются проектом.
Минимальные допустимые радиусы изгиба принимаются в соответствии с табл. 5.
Таблица 5
Диаметр трубопроводов, мм |
Минимально допустимые радиусы упругого изгиба трубопровода, м |
Диаметр трубопроводов, мм |
Минимально допустимые радиусы упругого изгиба трубопровода, м |
1400 |
1400 |
600 |
600 |
1200 |
1200 |
500 |
500 |
1000 |
1000 |
400 |
400 |
800 |
800 |
300 |
300 |
700 |
700 |
200 |
200 |
4.41. Упругий изгиб сваренного в нитку трубопровода следует выполнять непосредственно при его укладки в траншею, отрытую по проекту.
4.42. Гнутые отводы могут изготовляться в базовых, заводских условиях и непосредственно у места укладки в траншею из отдельных труб или двухтрубных секций.
4.43. Холодному гнутью подлежат только прямошовные и бесшовные трубы.
Унифицированные радиусы гнутых отводов устанавливаются в соответствии с табл. 6.
Таблица 6
Диаметр труб, мм |
Толщина стенки трубы, мм |
Унифицированные радиусы отводов при гнутье труб в холодном состоянии, м |
1420 |
16-20 |
60 |
1220 |
12-15 |
60 |
1020 |
10-14 |
40 |
720-820 |
8-12 |
35 |
529 |
7-10 |
25 |
426 |
6-12 |
20 |
219-377 |
4-25 |
15 |
Примечания:
1. Указанные радиусы относятся только к изогнутой части отвода. 2. Допускается отклонение величины радиуса на ±5%. |
|